Frames > More about framing > The birth of a frame
One of wood’s many vocations in life is to become a frame, but not any wood will do. The material is rigorously selected on the basis of its intrinsic qualities such as rigidity, porosity and hardness.
To guarantee its stability, the wood has to undergo two drying stages : one natural (three to six months) and one artificial (one to five weeks). A well-dried piece of wood is more stable and therefore, a prerequisite for the production of mouldings that should begin their lives straight and remain so.
The boards are cut into lengths before being shaped into mouldings. This operation is carried out by a machine known as a moulder. The lengths of dormant raw mouldings wait in our warehouses to be turned into any one of the infinite variations of frames available from Schleiper. This is where the know-how of skilled carpenters and modern technology complement one another, as the mouldings are electronically sawed to the right size and the mitred mouldings perfectly assembled.
Nail holes and joins are carefully filled in and the four pieces of moulding become a frame, albeit an unfinished one.
The surface of the raw frame has to be treated in accordance with the type of finish desired. If a stained, waxed, varnished or coated look is desired, the frame is first satin-smoothed with abrasive brushes.
If the frame is to be gilded or lacquered, then it needs an initial coat of gesso. This layer is sanded down meticulously until the surface is perfectly smooth. Once it has been washed and dried, the frame is ready for the next transformation.
A visit to the carver reveals that his profession has been collaborating with the framemaker’s for centuries. Ancient tools allow the wood to give birth to classical period ornaments. The carver’s skillful hands recreate the masterpieces of yesterday for the connoisseurs of today.
Other classical ornaments are reproduced and multiplied using stamps, cylindrical moulds and a special form of moulding dough. The techniques applied date back to the classical period but the ingredients for the dough change endlessly as new resins prove more resistant than the old.
The frame to be gilded is covered with a layer of bole in a specially equipped room. This coating is often a reddish colour, but can also be black, brown or green ... depending on the finish required. The bole is, as in the past, made from natural ingredients including clay, and serves to marry the precious metal leaves to the surface of the frame.
The gilders practise their art in a spacious area filled with workbenches. They apply the fragile, wafer-thin gold leaf that is only one hundredth of a millimetre thick, using cushions, palettes and gilding knives. Gilding today is carried out in the same manner it was centuries ago. It is a profession that requires a great deal of care, skill and concentration on the part of the crafts- man. The full reflective quality of gold-leaf on bole can only be obtained by polishing the frame using an agate stone. If a matt finish is required, the more modern process of gilding onto gold size produces excellent results.
For over three generations, our noble craftsmen and materials have conspired together to create timeless beauty.
The painting workshop conjures up marble, burr, shell, ivory and lapis-lazuli decorations at will; our craftsmen are masters in the art of creating the traceries of Renaissance interlacing and the volutes (curls) so dear to Horta and the Art Nouveau movement. If you have the necessary know-how, then your imagination can run riot.
Creative workers, carpenters, decorative painters and gilders work hard together to produce the body of the frame. It then has to be given a soul, an invented age and a past life, which is where the patina comes into play. Spots, wear, wax, worm holes or even a few fly specks can sometimes make all the difference. A succcessful frame, even if discreet, will show off the framed work in the best possible light.
As we move on upstairs, the workshop atmosphere changes, and aproned framers take over from the gold leaf gilders. Gloves are worn in order to protect your artworks and the work tables are covered in velvet. This is where your work of art meets its frame for the first time as well as its ideal companion – the mount. Chosen among a vast selection of colours, the mount is always cut out of high-quality , pH-neutral cardboard. This is also where expert hands go through the well-nigh sacred motions associated with picture framing : placing the work in the frame; introducing the cardboard and edging the glass and the back to ensure that the frame is airtight.
Finally, the finished work is inspected and packaged under the watchful eyes of our quality control staff. These are craftsmen who have worked for decades in our work- shops, and can assure that standards are not only maintained, but improved where possible.
The work of art is then ready to leave us and be returned to you for further enjoyment.
To guarantee its stability, the wood has to undergo two drying stages : one natural (three to six months) and one artificial (one to five weeks). A well-dried piece of wood is more stable and therefore, a prerequisite for the production of mouldings that should begin their lives straight and remain so.
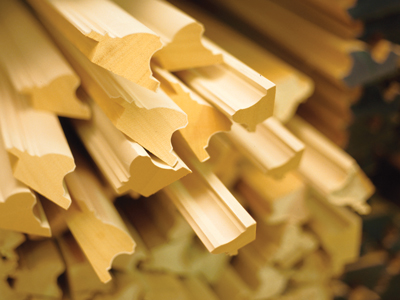
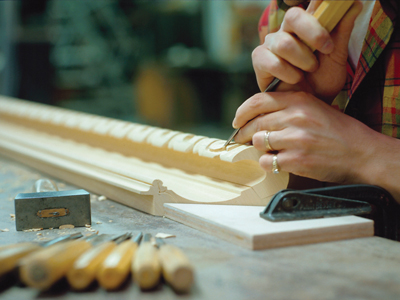
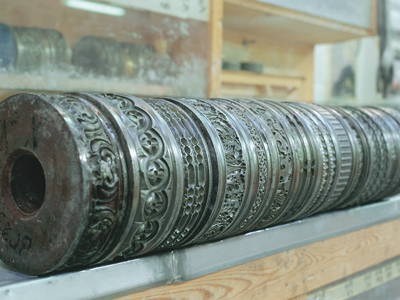
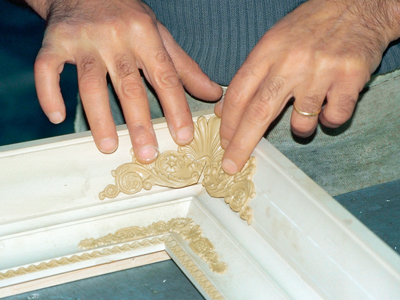
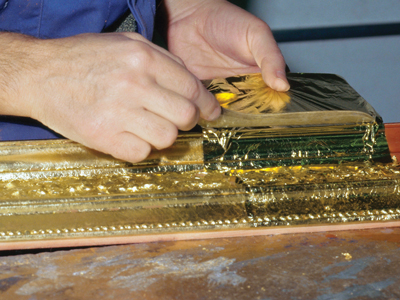
Nail holes and joins are carefully filled in and the four pieces of moulding become a frame, albeit an unfinished one.
The surface of the raw frame has to be treated in accordance with the type of finish desired. If a stained, waxed, varnished or coated look is desired, the frame is first satin-smoothed with abrasive brushes.
If the frame is to be gilded or lacquered, then it needs an initial coat of gesso. This layer is sanded down meticulously until the surface is perfectly smooth. Once it has been washed and dried, the frame is ready for the next transformation.
A visit to the carver reveals that his profession has been collaborating with the framemaker’s for centuries. Ancient tools allow the wood to give birth to classical period ornaments. The carver’s skillful hands recreate the masterpieces of yesterday for the connoisseurs of today.
Other classical ornaments are reproduced and multiplied using stamps, cylindrical moulds and a special form of moulding dough. The techniques applied date back to the classical period but the ingredients for the dough change endlessly as new resins prove more resistant than the old.
The frame to be gilded is covered with a layer of bole in a specially equipped room. This coating is often a reddish colour, but can also be black, brown or green ... depending on the finish required. The bole is, as in the past, made from natural ingredients including clay, and serves to marry the precious metal leaves to the surface of the frame.
The gilders practise their art in a spacious area filled with workbenches. They apply the fragile, wafer-thin gold leaf that is only one hundredth of a millimetre thick, using cushions, palettes and gilding knives. Gilding today is carried out in the same manner it was centuries ago. It is a profession that requires a great deal of care, skill and concentration on the part of the crafts- man. The full reflective quality of gold-leaf on bole can only be obtained by polishing the frame using an agate stone. If a matt finish is required, the more modern process of gilding onto gold size produces excellent results.
For over three generations, our noble craftsmen and materials have conspired together to create timeless beauty.
The painting workshop conjures up marble, burr, shell, ivory and lapis-lazuli decorations at will; our craftsmen are masters in the art of creating the traceries of Renaissance interlacing and the volutes (curls) so dear to Horta and the Art Nouveau movement. If you have the necessary know-how, then your imagination can run riot.
Creative workers, carpenters, decorative painters and gilders work hard together to produce the body of the frame. It then has to be given a soul, an invented age and a past life, which is where the patina comes into play. Spots, wear, wax, worm holes or even a few fly specks can sometimes make all the difference. A succcessful frame, even if discreet, will show off the framed work in the best possible light.
As we move on upstairs, the workshop atmosphere changes, and aproned framers take over from the gold leaf gilders. Gloves are worn in order to protect your artworks and the work tables are covered in velvet. This is where your work of art meets its frame for the first time as well as its ideal companion – the mount. Chosen among a vast selection of colours, the mount is always cut out of high-quality , pH-neutral cardboard. This is also where expert hands go through the well-nigh sacred motions associated with picture framing : placing the work in the frame; introducing the cardboard and edging the glass and the back to ensure that the frame is airtight.
Finally, the finished work is inspected and packaged under the watchful eyes of our quality control staff. These are craftsmen who have worked for decades in our work- shops, and can assure that standards are not only maintained, but improved where possible.
The work of art is then ready to leave us and be returned to you for further enjoyment.